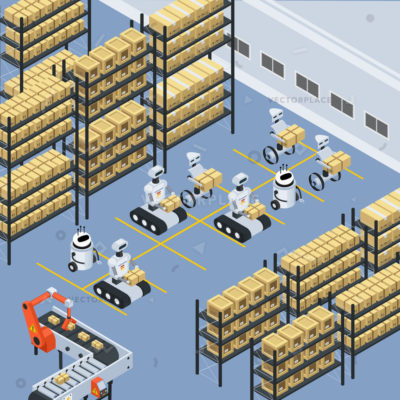
One of the biggest challenges facing the logistics industry today is labour availability. It’s not easy for companies around the world to find enough high-quality employees to move goods from suppliers to customers. Two competing factors are making this especially difficult and are driving smart warehouse market: The first is an increasing need for more logistics workers and this is being driven by the e-commerce revolution and its need for more parcel shipments; the second is a decline in the size of the available workforce due to shrinking population levels in the Western world.
This growth directly affects the requirement for logistics labor since online retail typically needs more labor per item sold than traditional brick-and-mortar retail. This is because, instead of moving merchandise to a retail store in bulk, the organization must pick and pack online purchases individually by hand. Freight and parcel handling labor goes up as well since these goods must be shipped as separate parcels to be delivered directly to consumers’ homes. Added to this, the average weight of these shipments is increasing as consumers can now order large items such as white goods, building supplies, and even furniture online. For the first time in history, future populations will be smaller than past generations in the mature markets. A recent study by BCG shows that over the next fifteen years Germany alone could see a labor deficit up to 10 million workers. This shortage of labor and skills is driving the smart warehouse market worth $30B by 2026.
Since 1948, the US economy has grown at an average pace of 3% per year. If this trend continues and with the current rate of productivity, over the next thirty years the US will need 35 million more workers than will be available. How will companies fill this labor gap?5 Even today employees are being asked to work additional years and retire later due to staff shortages, but logistics is a difficult occupation for an already aging workforce.
To combat these challenges, the managers of tomorrow’s supply chains will need to either continue to raise costs while reducing service or will need to compensate with automation that can support workers and increase productivity. Today’s current material handling automation solutions have helped to ease and postpone this challenge but in many cases the solutions are just not flexible enough to cover all of the requirements of a dynamic supply chain.
Research shows that 80% of current warehouses are manually operated with no supporting automation. These warehouses have dealt with demands for increased productivity and throughput by supporting existing workers with good layout design, mobile material handling equipment, and constantly improving IT.

Traditional Method
Semi Automated

Fully Automated
Some 15% of our current warehouses are mechanized. In addition to the technology used in manual warehouses, these distribution centers also use some type of material handling automation such as conveyors, sorters, goodsto-picker solutions, and other mechanized equipment to further improve the productivity of the existing workforce. While some of the components of these systems (ASRS / AGVs / shuttles) could be accurately considered as a type of robot, they are generally not in the same category as the robotic systems discussed so far in this trend report. The research finds that just 5% of current warehouses are automated and there is a huge adoption required for smart warehouse market.
The reality today is that these automated warehouses are typically highly mechanized environments that still employ people in key functions. An example would be a modern sorting center which has much higher productivity and accuracy than in previous generations. Even with all of this advanced technology, in large sorting hubs there may still be more than 1,000 employees who spend their time loading and unloading trucks, handling parcel ULD containers, and manually sorting odd-sized items.
A traditional warehouse employee typically spends most of his or her time walking around the warehouse to gather all of the items for an order. In a manual Amazon warehouse, a picker might walk between seven and fifteen miles per shift. As previously mentioned, to save labor by reducing the time spent walking, Amazon bought the company Kiva that builds mobile robots. These robots can pick up a shelf of goods and bring the entire shelf to the picker who stays in one spot, effectively turning these humans into stationary assembly line workers. After the picker selects the needed items, the shelf moves away and a different shelf arrives to take its place. This so-called goods-to-picker concept can be found in several technologies on the market today such as Swisslog´s CarryPick mobile system. It is possible in some cases to save 50% of warehouse picking labor with these systems through the elimination of walking. Currently, most of these systems are very capital intensive, requiring a network of connected shelves, tracks, robotic shuttles, elevators, and conveyors. Even after this investment, they still require a significant number of people to pick items from an automatically presented plastic tote or mobile shelf.
While these systems save walking, a relatively large labor force remains doing the very repetitive task of picking objects from one container and placing them into another. The companies that make the large goods-to-picker material handling systems have seen this problem as an opportunity to introduce robotic arms into their systems. An example is the German company SSI Schaefer that offers a product called Robo-Pick. This is a typical stationary industrial robot that is bolted inside a traditional robot work cell. The robot uses a camera to identify items in a plastic tote which has been delivered to the work cell by one of SSI Schaefer’s large automated tote storage and retrieval systems. Once the robot has located an item, it picks the product up and places it on a small buffer conveyor that will ultimately deposit the item in a separate transport tote. SSI Schaefer claims that its robot can pick up to 2,400 items per hour depending on product characteristics and order profile but it is just a part of automation as far as big opportunity of smart warehouse market is concerned.
Similar systems have been developed by the companies Knapp and Viastore. Knapp’s system can automatically change its vacuum cup gripper to better match the product, while Viastore’s system not only picks an item but can also place the item into a final shipping carton as well.
Mobile Piece Picking Robots
The opposite of the goods-to-picker system would be a mobile robot that drives around traditional warehouse shelves and picks items just like a person would. Several startup companies are currently working on robots that can do just that. IAM Robotics is a small company based in the United States. It is currently developing a mobile robot with an arm on top and a camera system that can navigate an existing warehouse and pick items from shelves and place them into an order tote. The system was first field tested in a pharmaceutical warehouse in New York where it was able to pick test orders from 40 items that it had never seen before. The robot will be tested next in a more general goods warehouse where it will be integrated with a warehouse management system (WMS) for the first time and pick live orders. IAM Robotics hopes to have a commercial version of its system available sometime.
The company Fetch Robotics is a well-funded startup that is also developing a robot that will drive around a warehouse picking items from shelves. Its primary robot, called Fetch, can extend its torso to reach upper shelves while a small secondary robot, call Freight, helpfully holds the tote that Fetch will pick items into. Each Fetch robot can have several of these smaller Freight robots supporting the picking process. The agile Freight robots quickly move the totes around the warehouse from area to area while the slower Fetch robots can stay in one aisle and focus on picking items. This effectively creates a hybrid of the goods-to-picker approach and the traditional manual picking concept. Fetch Robotics intends to also sell the smaller Freight robots separately; these can be used to help human workers in warehouses containing items that are too complicated for the Fetch robot.

Fetch Robot

Magazino Robot
Magazino is a German startup company that develops and builds perception-driven mobile robots for intralogistics. Its latest development is the picking robot TORU. Using 2D and 3D cameras and Magazino’s technology, this robot can identify individual objects on a shelf, grasp an item securely, and place it precisely at its destination. TORU works alongside humans, providing just-in-time object delivery to the workbench or shipping station. These are the latest addition in emerging smart warehouse market.
There are still technical and cost challenges to overcome before these robots will be ready for widespread use but they have some key advantages over stationary goods-to-picker robots. First of all, the concept is much more scalable. If you have a small distribution center, you may only need one or two mobile robots and you could add robots one at a time as you grow. One can even envisage renting or leasing the robots; the warehouse could first test a few of them during low times and later rent more during busy periods when more help is needed. These robots could work alongside existing workers, picking easy items while the humans pick the more complicated products or focus on solving exceptions. Moving to a new warehouse would be easier since the robots are not bolted to the floor and a market for used robots would develop, reducing investment risk.
Co-Packing and Customization
The next time that you walk through a grocery store, take a look at all of the different ways that products are displayed. You will see items with special ‘half off’ price stickers or you might see two items bundled together so that you can ‘buy one get one free’. Retailers have found that these modifications will catch our eye and cause us to buy more. This is a great sales device but it is expensive because adding all of these stickers, building the displays, and repackaging items takes a lot of labor and space. The retailers don’t want to deal with this extra labor so they have decided to push this problem to their suppliers. Now every major producer of shampoo, batteries, soup, and other merchandise is at risk of receiving requests to modify their products specifically for key customers, often with very little advanced warning. These last-minute modifications are often referred to as co-packing or customization.
In many cases, the customization process involves opening a box of products, taking out the items, doing something simple to them like putting on a sticker, and then packing the items back into the box. The processes are not normally difficult; they just take up space and require a lot of labor. The key to being a good co-packer is flexibility since every day means working with different products and slightly different modifications. Traditional industrial robots do not have this kind of flexibility so most co-packing is done manually.

Co-Picking Robot

Co-Picking Robot
LogisticsIQ™’s latest market research study “Warehouse Automation Market By Technology (AGV/AMR, AS/RS, Conveyors, Sortation, Picking (incl. Automatic Identification and Data Capture), Robotics, Palletizing & Depalletizing, Overhead Systems, Services and Software), By Industry (E-commerce, General Merchandise, Grocery, Apparel, Food & Beverage, Pharma, 3PL), By Functions (Inbound, Picking, Outbound), By Geography – Global Forecast to 2025“, estimates that the global Warehouse Automation Market will grow almost double from $13 Billion in 2018 to $27 billion by 2025, at a CAGR of 11.7% between 2019 and 2025. Visit our page on Smart Warehouse Market for more details.